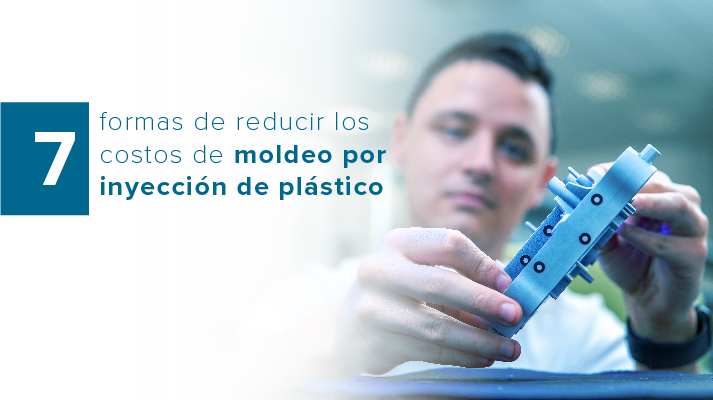
El moldeo por inyección es una forma rentable de producir piezas, pero a menudo hay una cantidad significativa de desecho involucrada, desde ineficiencias hasta errores del usuario, daño de la máquina y tiempo de inactividad, altas tasas de desecho y más. Aquí hay 7 formas de reducir sus costos de moldeo por inyección para que pueda mejorar sus resultados.
1. Reducir el riesgo y el costo de la calidad
Los aspectos de reducir el riesgo y el costo de la calidad suelen ser reactivos en lugar de proactivos. Esto ocurre porque el desarrollo de procesos de moldeo por inyección capaces de manejar variaciones anormales imprevistas puede ser muy difícil de predecir. Esto nos expone a riesgos y gastos imprevistos debido a la entrega de piezas inaceptables.
Hay una forma mejor. Empiece por utilizar principios científicos de moldeo para desarrollar un proceso robusto y repetible. Una vez que el proceso se ha desarrollado utilizando sensores y tecnología, usted puede monitorear una amplia variedad de defectos comunes en el moldeo por inyección para garantizar el 100% de calidad a sus clientes.
Cuántas veces hemos visto este escenario: Una prensa ha estado funcionando durante semanas y los técnicos de proceso están haciendo ajustes continuamente. La calidad ahora nos alerta de un defecto en las piezas, por lo que tenemos que ajustar el proceso nuevamente para corregir el defecto, poner en cuarentena el producto sospechoso y clasificar, triturar o reelaborar los componentes defectuosos.
En el peor de los casos, hemos enviado algunos de los componentes al cliente y tenemos que alertarle del problema. Los costos en esta situación son numerosos. Al no desarrollar y documentar un proceso sólido basado en principios científicos de moldeo, nuestros técnicos dedican su valioso tiempo a ajustar el proceso para esperar crear una buena pieza.
Una vez que se descubre el defecto, los técnicos vuelven a llamar a la prensa para corregir el problema, y existe la incertidumbre de si el problema volverá a ocurrir. Ahora tenemos que averiguar qué hacer con el producto; clasificar o reelaborar puede llevar días o semanas y rara vez es 100% efectivo. Sin mencionar que es una tarea sin valor agregado, porque no podemos inspeccionar la calidad de la pieza.
Si estas piezas han llegado al cliente, el costo puede ser una pérdida de negocio. Esta situación podría haberse evitado si hubiéramos invertido el tiempo por adelantado para crear y documentar un proceso que es capaz repetidamente de producir piezas de calidad. El uso de sensores de presión en la cavidad para monitorear el proceso puede agregar un mayor nivel de control. Imagínese saber antes de que se abra el molde si la pieza es buena o mala y poder clasificar esa pieza automáticamente.
2. Aumente la eficiencia mediante la automatización
Con tecnología y capacitación, usted puede automatizar varias áreas de producción para ayudar a que la fuerza laboral sea más eficiente. La selección, el apilado y el paletizado de piezas son tres tipos de automatizaciones útiles. La tecnología de control de procesos puede permitir la clasificación automática de piezas y alarmas para avisarle cuando un proceso esté fuera de tolerancia. Esto mejora aún más la eficiencia y la precisión al proporcionar datos que le permiten determinar las causas raíz más rápidamente sin señalar con el dedo. Puede suspender la localización de averías y comenzar a eliminar problemas.
Piense en los procesos en una instalación sin automatización. Pasando por el proceso, tenemos que retirar la pieza y el sistema de canal del molde, organizar las piezas para empaquetarlas, empacar y luego paletizar el producto final. En algún lugar de ese proceso, puede agregar un paso de ensamblaje que agregará mano de obra, espacio de piso y tiempo adicionales.
Si estos procesos se realizan con mano de obra, siempre habrá una cantidad variable de eficiencia en el proceso. Si nos enfocamos solo en retirar las piezas del molde, incluso los operadores más consistentes causarán variaciones en el tiempo del ciclo, lo que conduce a variaciones en la calidad de las piezas. Esto se agravará a través de cada paso del proceso.
A medida que comenzamos a automatizar el proceso, comenzamos a eliminar las inconsistencias, aumentar la eficiencia, mejorar la calidad y aumentar el espacio disponible. Automatizar la calidad, ya sea a través de del monitoreo de procesos, los sistemas de visión o la verificación dimensional en línea, puede garantizar que nuestros clientes nunca más reciban un producto defectuoso.
3. Aumente el conocimiento de la variación del proceso (reduzca el desecho)
Al saber inmediatamente cuándo se ha producido una variación en un proceso, puede solucionar los problemas antes. Eso significa menos desechos, lo que permite una mayor utilización del tiempo disponible de la máquina y menos dinero tirado a la basura. Puede hacerlo a través del software de control de procesos, el monitoreo de la presión de la cavidad y la capacitación.
En la fabricación, siempre existe un costo inherente a la calidad. Se puede incurrir en este costo al final de la producción mediante el uso de recursos valiosos y tiempo para inspeccionar las piezas antes de que puedan enviarse al cliente. El problema es que nunca obtenemos un costo fijo de calidad. A medida que varía la producción, también varía el tiempo de clasificación y la cantidad de empleados necesarios para clasificar el producto.
Si la rotación de empleados es un problema, se debe hacer una inversión en capacitar a los nuevos empleados para que solucionen los defectos. Al asegurarse de que todo el personal técnico esté capacitado con el mismo estándar, puede ser proactivo para reducir o eliminar los rechazos en lugar de reactivar y combatir los altos niveles de desecho debido a los bajos niveles de habilidad y los procesos mal configurados con ventanas de proceso pequeñas o inexistentes.
Otra forma de ver el costo de la calidad es primordial. Al incorporar la calidad a un proceso y monitorear la calidad a lo largo del ciclo, podemos detectar cuándo puede ocurrir una variación en el proceso. Por ejemplo, si sabemos que un material tiene un cambio de viscosidad amplio que causa problemas con la calidad, podemos usar herramientas de monitoreo de procesos para detectar un cambio de viscosidad. En este punto, el proceso se puede volver a centrar para volver a hacer componentes de calidad.
4. Compre resina de amplia especificación
La resina que tiene más variación en las propiedades es más barata, pero puede ser difícil validar o mantener las dimensiones con piezas de tolerancia ajustada. Esto puede aumentar la variabilidad y, por lo tanto, las tasas de desechos, pero si usamos técnicas de DECOUPLED MOLDING® (MOLDEADO DESACOPLADO®) junto con sensores en el molde, esto puede ser una empresa exitosa.
Cuántas veces ha visto este escenario: Usted tiene una buena producción durante días y, de repente, comienza a ver flash en las piezas. Para solucionar el problema, el técnico de proceso reduce la velocidad de llenado. Unas horas más tarde, la calidad le llega a usted con tomas cortas. ¿Por qué de repente tenías buenas partes y luego instantáneamente usted tuvo flash? Lo más probable es que la respuesta sea la viscosidad.
La viscosidad a menudo puede oscilar un 30% en cualquier dirección, lo que dificulta la fabricación de una buena pieza, incluso con un proceso Decoupled II (Desacoplado II). Para garantizar que se fabriquen las mismas piezas en cada ciclo (o al menos con la frecuencia que podamos), se deben utilizar sensores de presión de cavidad para controlar el proceso y minimizar los impactos de los cambios de viscosidad en el material.
5. Menor tiempo de ciclo
Puede utilizar el moldeado científico y las técnicas DECOUPLED MOLDING® (MOLDEADO DESACOPLADO®) para optimizar los movimientos de sujeción/expulsión, el tiempo de llenado, el tiempo de empaque, el tiempo de retención y el enfriamiento. Solo puede usar lo que se necesita para hacer buenas piezas con un búfer más pequeño.
Las unidades de control de temperatura del molde de tamaño adecuado, o termolatores, también ayudarán a reducir los tiempos de ciclo. El 80% del ciclo de moldeo se gasta enfriando la pieza desde la temperatura de fusión hasta una temperatura de expulsión en la que la pieza es lo suficientemente rígida para resistir las fuerzas de expulsión y mantener la integridad dimensional. Si no tenemos suficiente flujo de agua, la capacidad de enfriar la pieza a la temperatura correcta se ve comprometida, y la solución es dejar la pieza en el molde por más tiempo, lo que cuesta más dinero.
La evaluación del espesor de la pieza al comienzo del proyecto es el primer paso para determinar el tiempo de ciclo. Es importante cuestionar el grosor de la pieza y cómo afecta el tiempo de ciclo y el rendimiento de la pieza. A menudo, encontramos que las piezas se han diseñado de esta manera porque “así es como siempre lo hemos hecho”. Como puede imaginar, esto puede resultar muy costoso. La ciencia y la simulación ayudan a predecir el éxito del diseño, por lo que ya no necesitamos construir y probar para obtener resultados. Garantizar el diseño adecuado de las piezas es solo un ejemplo de cómo puede reducir el tiempo de ciclo general.
6. Construya moldes más eficientes
En pocas palabras, un molde es un recipiente a presión y un intercambiador de calor; siempre habrá una pérdida de presión dentro de la cavidad. Sin embargo, en la mayoría de los casos, cuanto menor sea la pérdida de presión desde la post compuerta hasta el final de la cavidad, es menos probable que tengamos problemas de calidad como deformaciones, vacíos, hundimientos, tomas cortas o variación dimensional.
Para hacer que el plástico fluya necesitamos calentarlo, pero para expulsarlo necesitamos eliminar algo de ese calor. Para construir un molde efectivo, es vital asegurarse de que las líneas de agua estén colocadas en la ubicación correcta. También debemos seleccionar un metal que transfiera bien el calor pero que también pueda soportar el material (específicamente material con relleno de vidrio o fibra de carbono). Por último, el proceso debe configurarse con un flujo de agua turbulento para garantizar que el molde pueda alcanzar la estabilidad térmica rápidamente y mantener esa estabilidad durante un largo ciclo de producción.
Usted también puede mejorar la eficiencia del molde aumentando la cavitación. Los moldes de una cavidad ofrecen la menor cantidad de variabilidad, sin embargo, el precio de producir una sola pieza a la vez es extremadamente alto. Si puede pasar a una cavitación más alta, puede producir más piezas en la misma cantidad de tiempo. Existen limitaciones en la cantidad de cavidades que puede tener, incluida la calidad, el espacio entre moldes y máquinas y los requisitos de validación.
Otra forma de mejorar la eficiencia del molde es construir moldes familiares, que incluyen diferentes geometrías de piezas en el mismo molde. Esto puede ser extremadamente difícil, porque las cuatro variables de plástico difieren dentro de cada cavidad. Sin embargo, con el software de control de procesos y los sensores en molde, puede usar compuertas de válvula para controlar cada cavidad de forma independiente.
7. Reduzca los costos de transferencia de moldes
Las aplicaciones de desarrollo de procesos garantizan que pueda transferir rápida y fácilmente un molde de una máquina a otra. Las hojas de configuración específicas de la máquina se generan automáticamente cuando se transfiere el molde, por lo que puede producir buenas piezas desde el primer disparo. Esas curvas se pueden utilizar en cualquier máquina siempre que la máquina sea capaz de proporcionar un caudal, presiones, temperaturas y volúmenes adecuados O si no se utiliza la simulación, podemos generar plantillas y transferirlas a cualquier máquina capaz.
Ahorre tiempo, energía y recursos al no tener que crear sus propias herramientas de conversión no reguladas o recrear el proceso desde cero para cada nueva máquina.