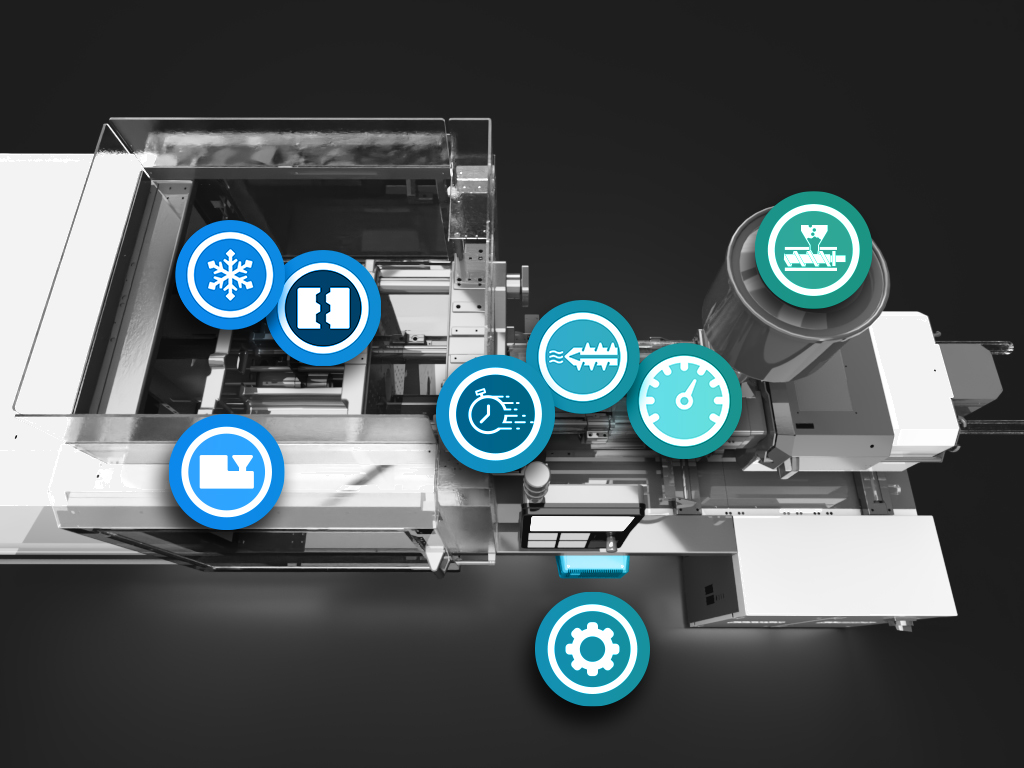
Hablamos mucho sobre la optimización del proceso de moldeo por inyección, pero ¿en qué consiste exactamente? ¿Qué parámetros deben perfeccionarse para lograr una optimización máxima? Aquí están los 8 parámetros clave en el moldeo por inyección que deben alinearse para producir piezas de plástico consistentes y de alta calidad.
1. Control de Temperatura:
Temperatura del Plástico o Fusión: El control adecuado de la temperatura del plástico es esencial para fundirlo de manera uniforme. Los diferentes materiales tienen requisitos de temperatura específicos, y mantener el rango de temperatura correcto evita problemas como la fusión incompleta o la degradación térmica.
Temperatura del Molde: Controlar la temperatura del molde afecta la cristalinidad, contracción y tiempo del ciclo de la pieza. Mantener el molde a la temperatura recomendada ayuda a garantizar que la resina tenga las características mecánicas correctas.
2. Velocidad de Inyección:
La velocidad a la que se inyecta el plástico fundido en el molde afecta el patrón de llenado, la densidad de la pieza y la calidad general. La velocidad de llenado también tiene un efecto en la fase de embalaje del proceso de moldeo. Ajustar la velocidad de inyección ayuda a prevenir problemas como líneas de flujo o trampas de aire.
3. Tiempo de Enfriamiento:
El tiempo de enfriamiento es la duración que la pieza pasa en el molde después de que el material se ha llenado y empaquetado. El tiempo de enfriamiento adecuado es crucial para evitar deformaciones y garantizar que la pieza se solidifique de manera uniforme. También influye en el tiempo total del ciclo del proceso de moldeo por inyección.
4. Selección del Material Plástico:
La elección del material plástico tiene un impacto significativo en el proceso de moldeo por inyección. Los diferentes materiales tienen puntos de fusión, tasas de contracción y características de flujo variables. Seleccionar el material apropiado para la aplicación prevista es esencial para lograr las propiedades deseadas de la pieza.
5. Velocidad y Contrapresión del Tornillo:
Velocidad del Tornillo: La velocidad de rotación del tornillo en la máquina de moldeo por inyección afecta la cizalladura general del material. La velocidad del tornillo debe seleccionarse según el tipo de material y el contenido aditivo. La velocidad correcta del tornillo asegurará que la rotación del tornillo y la geometría del tornillo proporcionen la cantidad correcta de cizalladura.
Contrapresión: Mantener la contrapresión adecuada en el tornillo garantiza una mezcla y homogeneización adecuadas del plástico fundido. También ayuda a prevenir huecos y mejorar la calidad de la pieza.
6. Calibración de la Máquina de Inyección:
La calibración regular de la máquina de moldeo por inyección es crucial para mantener la precisión en el proceso. Esto incluye la calibración de la presión, temperatura y configuraciones de tiempo de la máquina.
7. Diseño y Mantenimiento del Molde:
Los moldes bien diseñados con ventilación, compuertas y canales de enfriamiento adecuados contribuyen significativamente al proceso de optimización. El mantenimiento regular de los moldes es esencial para evitar problemas como desgaste, corrosión o daños que puedan afectar la calidad de la pieza.
8. Sistemas de Monitoreo y Control:
Implementar sistemas avanzados de monitoreo y control (como CoPilot®) permite el seguimiento en tiempo real de varios parámetros. Esto permite la rápida identificación de desviaciones y facilita acciones correctivas rápidas, contribuyendo a la mejora continua en el proceso de moldeo por inyección.
Conclusión
Optimizar el proceso de moldeo por inyección es una tarea multifacética que involucra una atención meticulosa a varios parámetros. Ajustando la temperatura, presión, velocidad y otros factores clave, se pueden lograr resultados consistentes y de alta calidad mientras se minimizan los defectos y los tiempos de ciclo. A medida que avanza la tecnología, la integración de sistemas inteligentes y monitoreo en tiempo real mejora aún más la eficiencia y confiabilidad de los procesos de moldeo por inyección. Los esfuerzos continuos en la optimización del proceso contribuyen al éxito general y la competitividad de las industrias de fabricación de plástico.