Vea lo que está ocurriendo dentro del molde para mejorar la uniformidad y la calidad de las piezas
Recopilar información del interior de la cavidad, en el centro del proceso, le proporciona la información necesaria para garantizar la calidad de cada disparo.
Solicite una consulta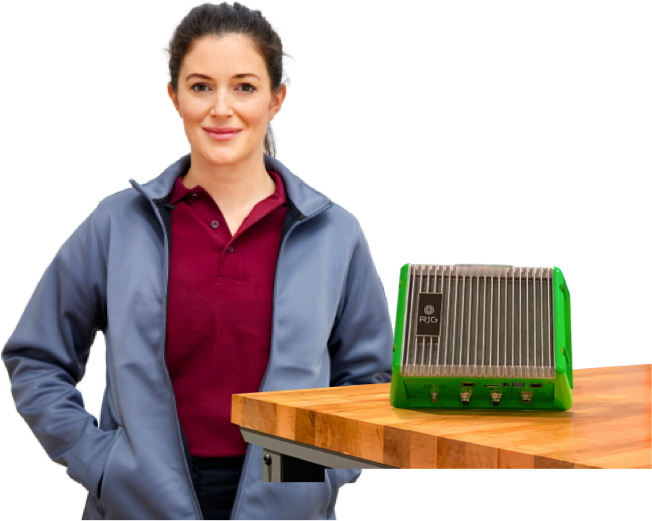
Aproveche el poder del conocimiento con la tecnología de sensores para el moldeo por inyección
La presión de cavidad es la variable del proceso más directamente relacionada con la calidad de las piezas, ya que se mide donde estas se producen.
- Conozca cuando cambie un proceso y sepa cómo volver a ajustarlo utilizando datos del interior de la cavidad
- Reduzca el tiempo necesario para producir piezas buenas
- Haga un seguimiento de la variación para eliminar las suposiciones durante la resolución de problemas
- Reduzca los costos de validación validando los procesos de manera independiente de la máquina
- Archive y exporte datos críticos
- Cree una pista de auditoría para reducir los riesgos de cada pieza enviada
- Entérese de inmediato cuando algo cambie en su proceso
- Separe automáticamente las piezas anormales y elimine las inspecciones manuales
- Deje de enviar piezas defectuosas a sus clientes
- Controle de forma precisa y constante el proceso de moldeo
- Reduzca los desechos y mejore la calidad de las piezas
- Prolongue la vida útil de la herramienta y reduzca los daños al equipo
Tipos de tecnologías de sensores para el moldeo por inyección
Sensores de presión de cavidad
Los sensores de presión de cavidad le permiten construir un proceso en torno a lo que realmente está sucediendo en el molde. Los datos de presión también pueden ayudar a identificar problemas comunes de moldeo, tales como disparos cortos, dimensiones, hundimientos, rebabas, deformaciones y más.
Sensores de temperatura
La temperatura es crítica para la fabricación de muchas piezas, en especial las que se fabrican con materiales semicristalinos o con tolerancias dimensionales estrechas. Los cambios o las interrupciones del tiempo de ciclo, las líneas de enfriamiento obstruidas o la configuración inadecuada del enfriamiento pueden afectar drásticamente la estabilidad térmica. Los sensores de temperatura en la cavidad le ayudan a diagnosticar problemas y prevenir el envío de piezas defectuosas.
Sensores de deformación del molde
Los sensores de deformación del molde miden cuánto se abre la línea de separación del molde en cada ciclo, lo cual ayuda a detectar problemas relacionados con el ajuste adecuado del tonelaje de cierre, la rebaba o incluso el gas atrapado si los respiraderos se colapsan debido a una fuerza de cierre excesiva. También pueden utilizarse en aplicaciones en las que no es posible emplear sensores de presión de cavidad.
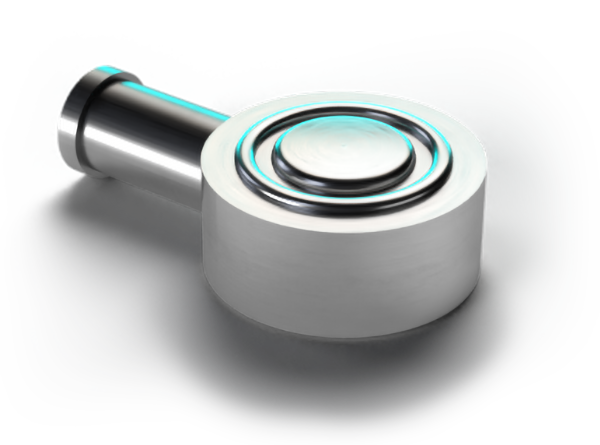
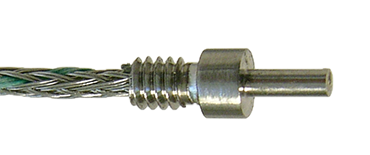
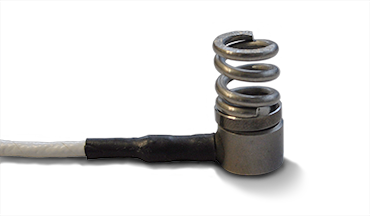
Tipos de sistemas de sensores de presión de cavidad
Sensores Lynx® de un solo canal
Nuestros sensores digitales Lynx son los sensores de presión de cavidad más precisos y fáciles de usar disponibles en la actualidad. Los algoritmos únicos integrados en cada unidad mejoran considerablemente la precisión de estos sensores. Estos sensores "inteligentes" también incluyen otros datos de calibración clave para simplificar la configuración y el uso diario en la planta.
Estos sensores son ideales para las aplicaciones en moldes con menos cavidades en las que se requieren cuatro o menos sensores. Los sensores Lynx de un solo canal están disponibles con galga extensiométrica o con tecnología de sensores piezoeléctricos.
Sensores empotrados Lynx
Diseñados para moldes con cavidades más altas, los sensores empotrados Lynx brindan todos los beneficios del sensor Lynx de un solo canal, pero los componentes electrónicos y el cabezal del sensor están totalmente empotrados en el molde, lo que proporciona un solo punto de conexión en la parte lateral del molde y elimina el cableado externo.
Beneficios de los sensores empotrados Lynx:
- Reducción de los daños durante el uso y el mantenimiento de la herramienta
- Reducción del espacio ocupado y el cableado en la parte lateral del molde
- Adecuados para aplicaciones de sensores de presión de cavidad mediana a alta (4-31)
Sistema de conexión multicanal de galga extensiométrica
Este sistema de hardware robusto y de bajo perfil simplifica la instalación en moldes con cuatro o más sensores estilo botón y ahorra espacio en el molde. Le permite conectar hasta ocho sensores con galgas extensiométricas a un punto de conexión en el molde, lo que reduce el espacio que ocupa el hardware y ahorra costos. El Mold-ID identifica los sensores y el molde con los sistemas CoPilot y eDART, por lo que usted puede estar seguro de tener el molde correcto funcionando y los sensores correctos seleccionados.
Beneficios de los sensores de galgas extensiométricas multicanal y Mold-ID:
- Reducción del espacio ocupado en los moldes multicavidad
- Robustos y de bajo perfil
- Ahorro de costos en comparación con otras soluciones multicavidad
- Instalación simplificada
Sistema piezoeléctrico multicanal
El sistema de presión de cavidad piezoeléctrico multicanal permite a los moldeadores por inyección conectar hasta ocho sensores piezoeléctricos a un punto de conexión en el molde. La interfaz con Mold-ID identifica los sensores y el molde con los sistemas CoPilot y eDART, por lo que usted puede estar seguro de tener el molde correcto funcionando y los sensores correctos seleccionados.
Beneficios de los sensores piezoeléctricos multicanal:
- Reducción del espacio ocupado en los moldes multicavidad
- Robustos y de bajo perfil
- Instalación simplificada
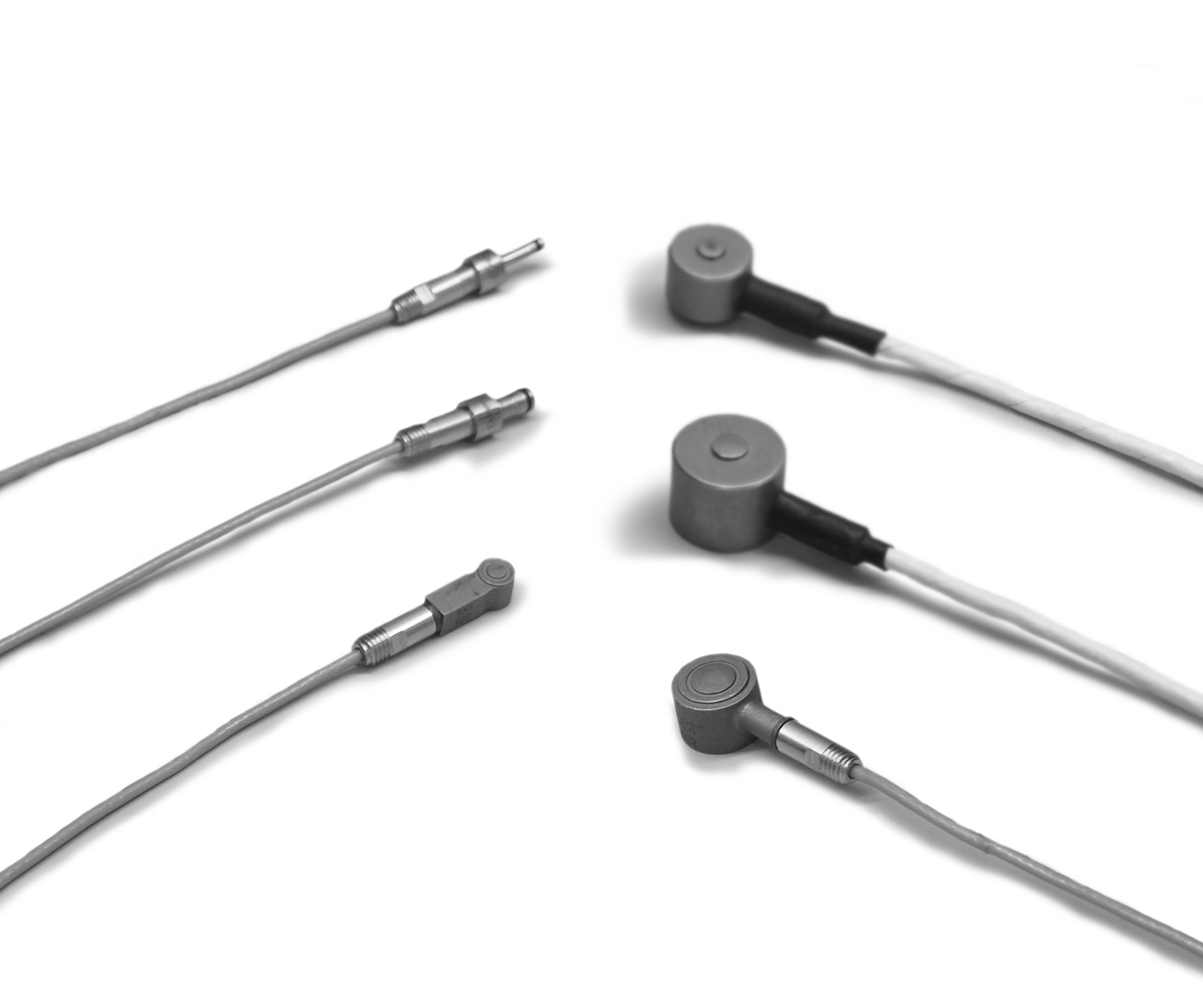
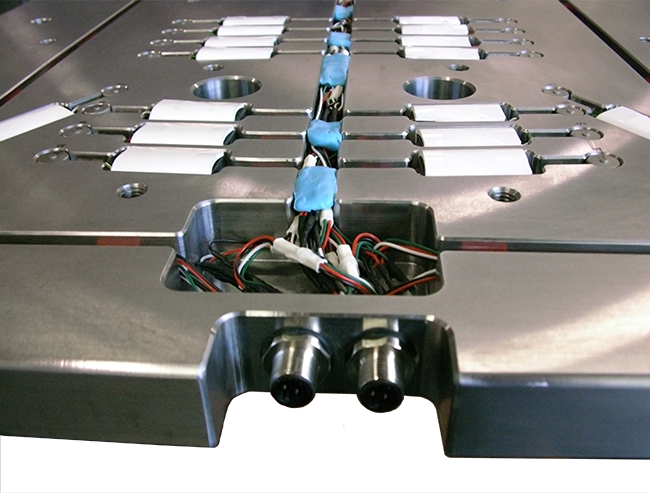
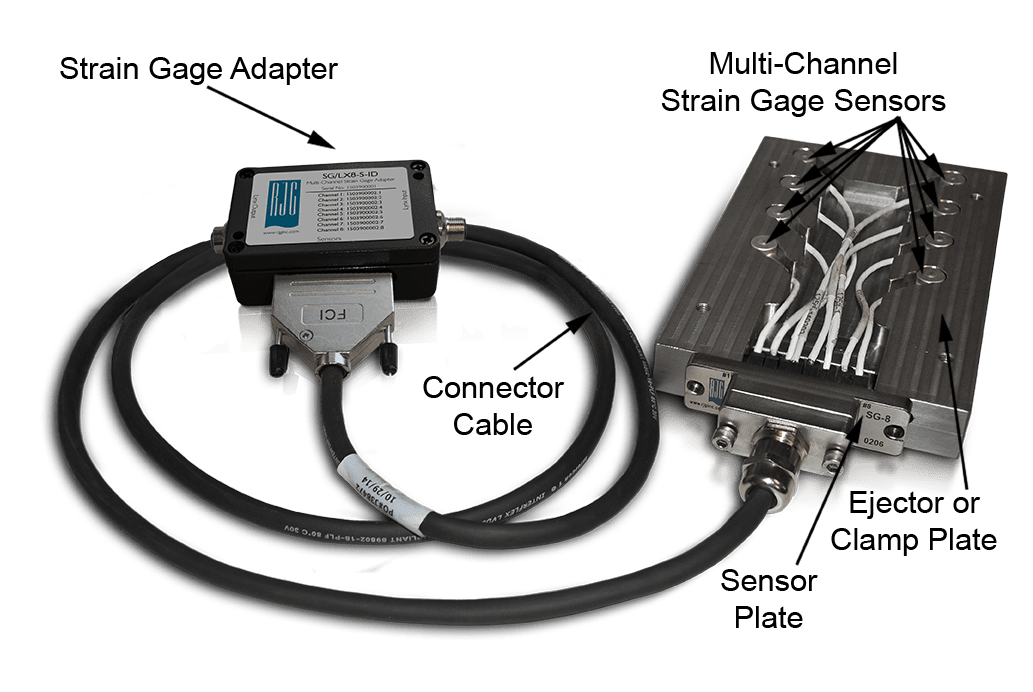
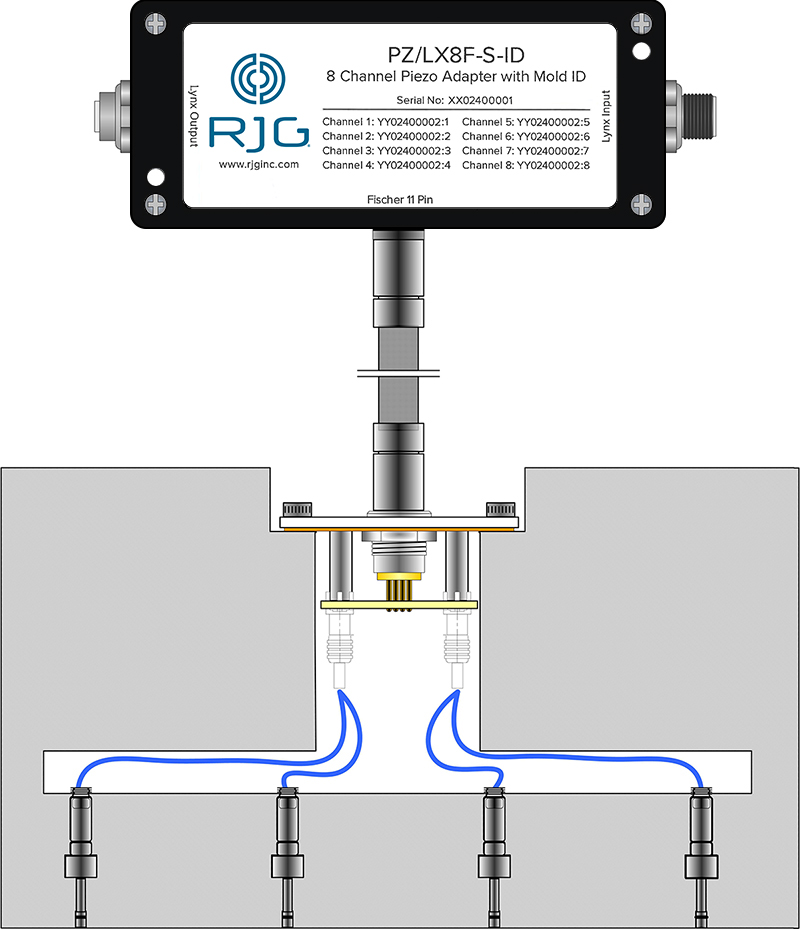
Estamos aquí para garantizar que sus sensores funcionen correctamente
Selección del sensor
Elegir el sensor adecuado es fundamental para una instrumentación exitosa. Le daremos recomendaciones personalizadas con respecto a los sensores para que cuente con la información precisa que necesita por adelantado.
Estrategias de implementación
Las técnicas de colocación e instalación de sensores pueden afectar en gran medida la precisión y la eficiencia de sus resultados. Nos aseguraremos de que recopilen los datos vitales para su proceso.
Probadores de sensores
Los sensores mal instalados o dañados pueden hacer que salgan piezas defectuosas y ocasionar un costoso tiempo de inactividad de las máquinas. Los probadores de sensores le permiten garantizar que los sensores funcionen de forma correcta y precisa antes de que la herramienta vaya a la prensa.
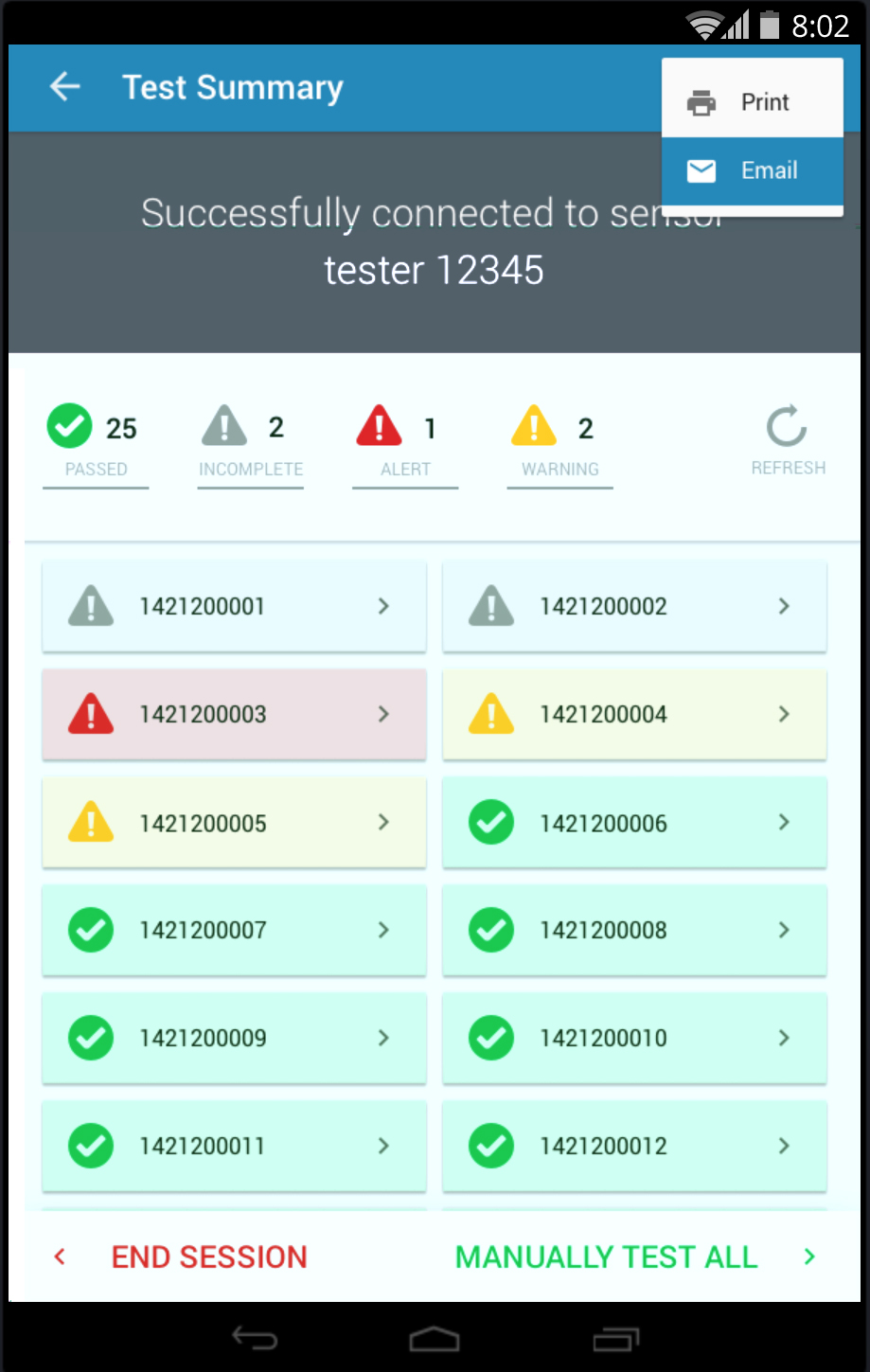
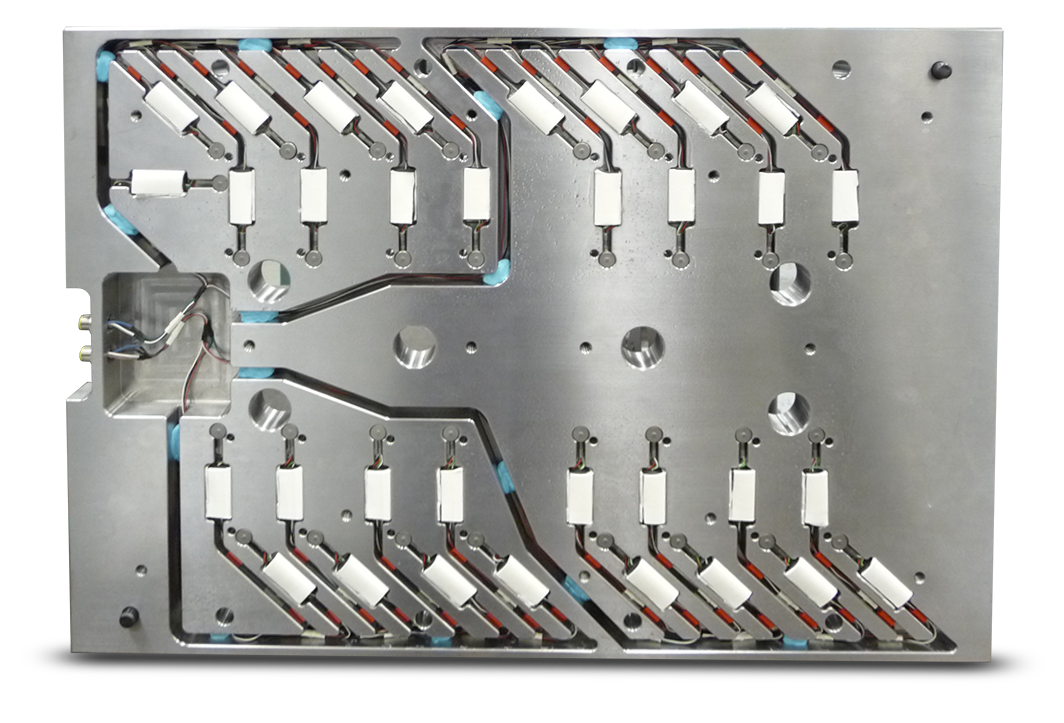
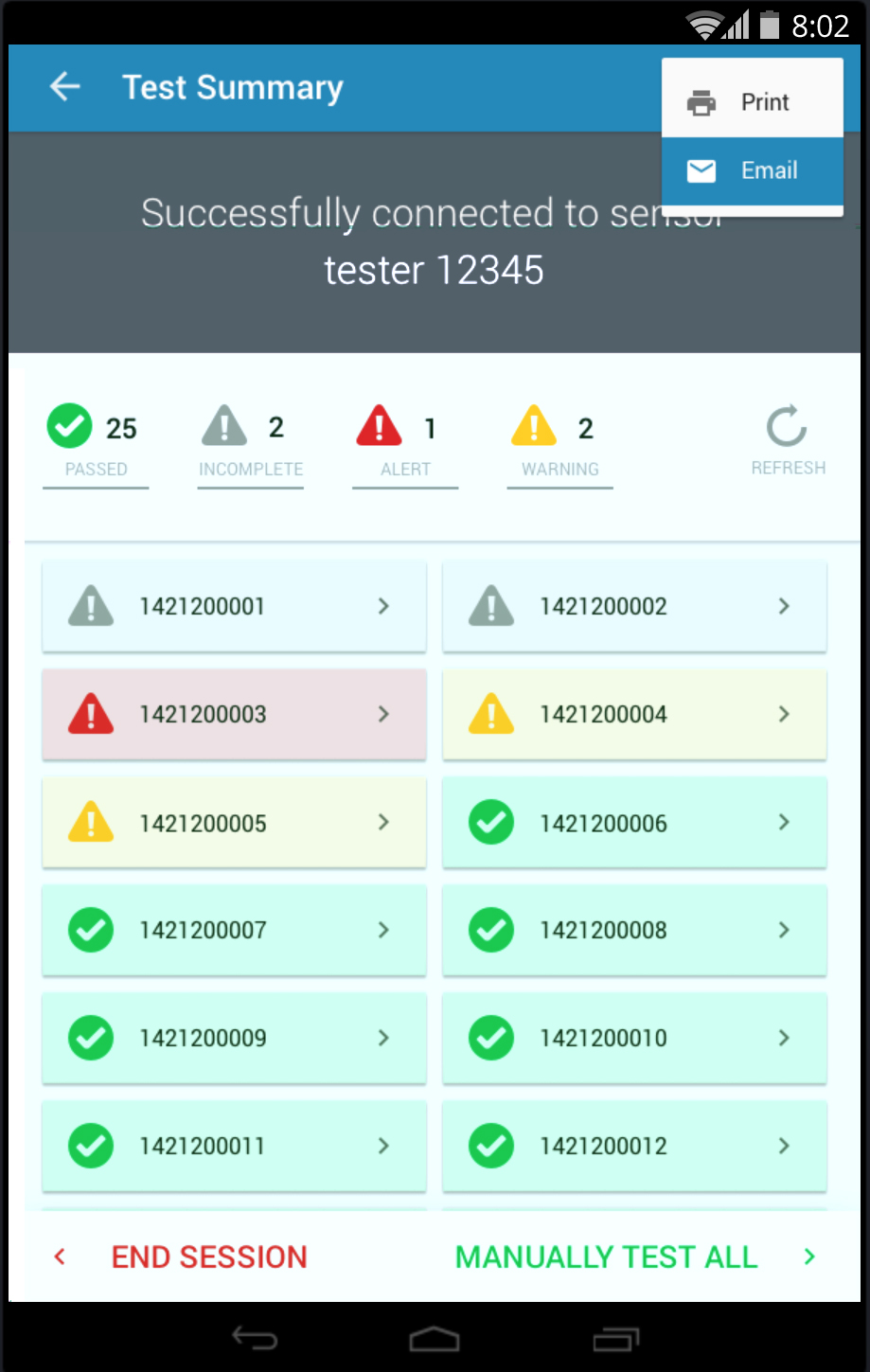
Testimonios
Hear what our amazing customers have to say about in-mold sensors:
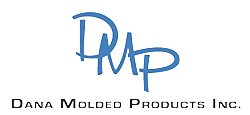
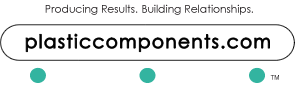
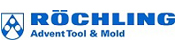
Validación confiable de piezas médicas moldeadas
Nuestros clientes tienen un claro entendimiento de lo que RJG nos permite ver, comprender y documentar, lo que claramente les proporciona un mayor nivel de confianza de que su producto es el mejor posible
Fred Chamberlain
Vicepresidente de operacioness Dana Molded Products
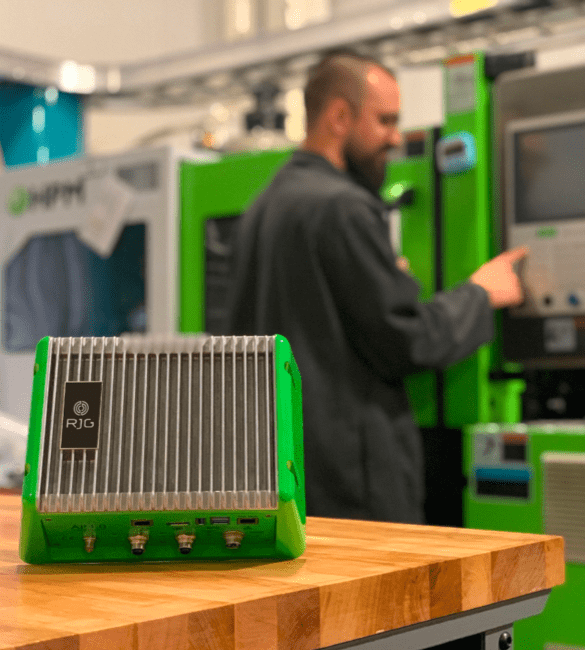
Es como tener un auditor de tiempo completo en cada prensa
RJG nos ha proporcionado mejoras de calidad y ahorros en costo. Al usar el software, podemos reducir la frecuencia de los controles de calidad necesarios para garantizar piezas buenas. Usar el sistema eDART y sensores dentro del molde es como tener un auditor de tiempo completo en cada prensa.
Chris Laverty
Ingeniero de fabricación Plastic Components, Inc.
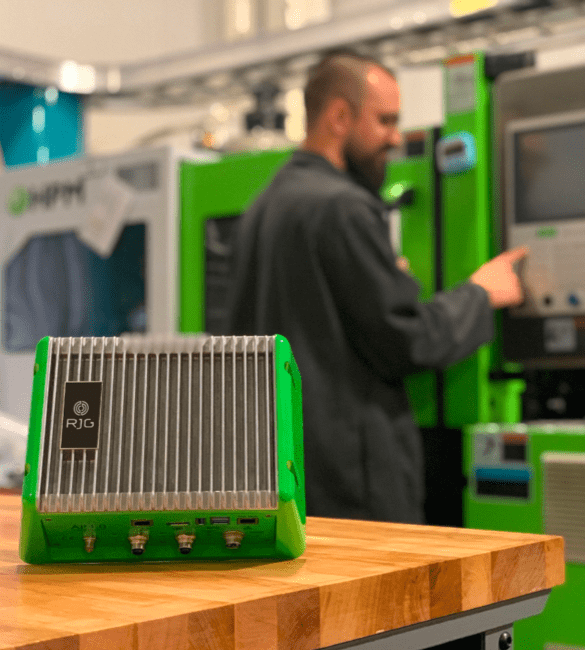
Calidad una y otra y otra vez
Un molde de 16 cavidades diseñado y construido por Advent que incorpora un sensor de presión de cavidad en cada una de ellas… Desde que Advent comenzó a producir esta pieza hace más de 5 años y 250 millones de piezas, no hemos enviado una sola pieza defectuosa a los clientes.
Ken Desrosiers
Presidente Advent Tool and Mold Co.
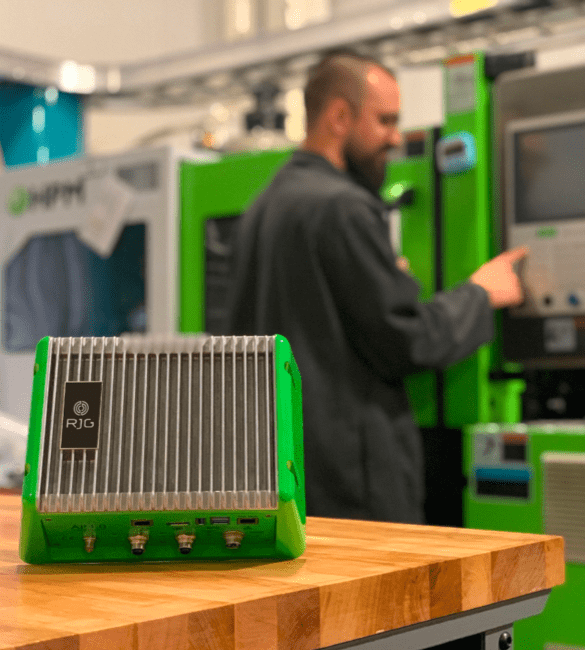
Recursos sobre los sensores
Ver más información sobre estos productos
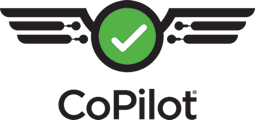
COPILOT
CoPilot es la tecnología inteligente más moderna de moldeo por inyección. Este sistema simple y fácil de usar hace que sea más fácil que nunca asegurarse de que sus clientes solo reciban piezas de la más alta calidad, mientras se minimiza el desperdicio en el proceso.

THE HUB
The Hub es un servidor de red que reúne todos los datos de CoPilot en un solo lugar. The Hub incluye un sistema de gestión de datos para registrar datos de procesamiento y una base de datos para almacenar las especificaciones de los procesos, las máquinas y los moldes.

PROCESADOR DE APLICACIONES 4.0
El procesador de aplicaciones AP4.0 es una computadora industrial de cuatro núcleos y bajo consumo de energía, diseñada para tareas de uso intensivo del procesador y con tecnología Lynx de RJG integrada. La carcasa de aleación de aluminio del AP4.0 fue diseñada para funcionar en las condiciones de fabricación más duras.
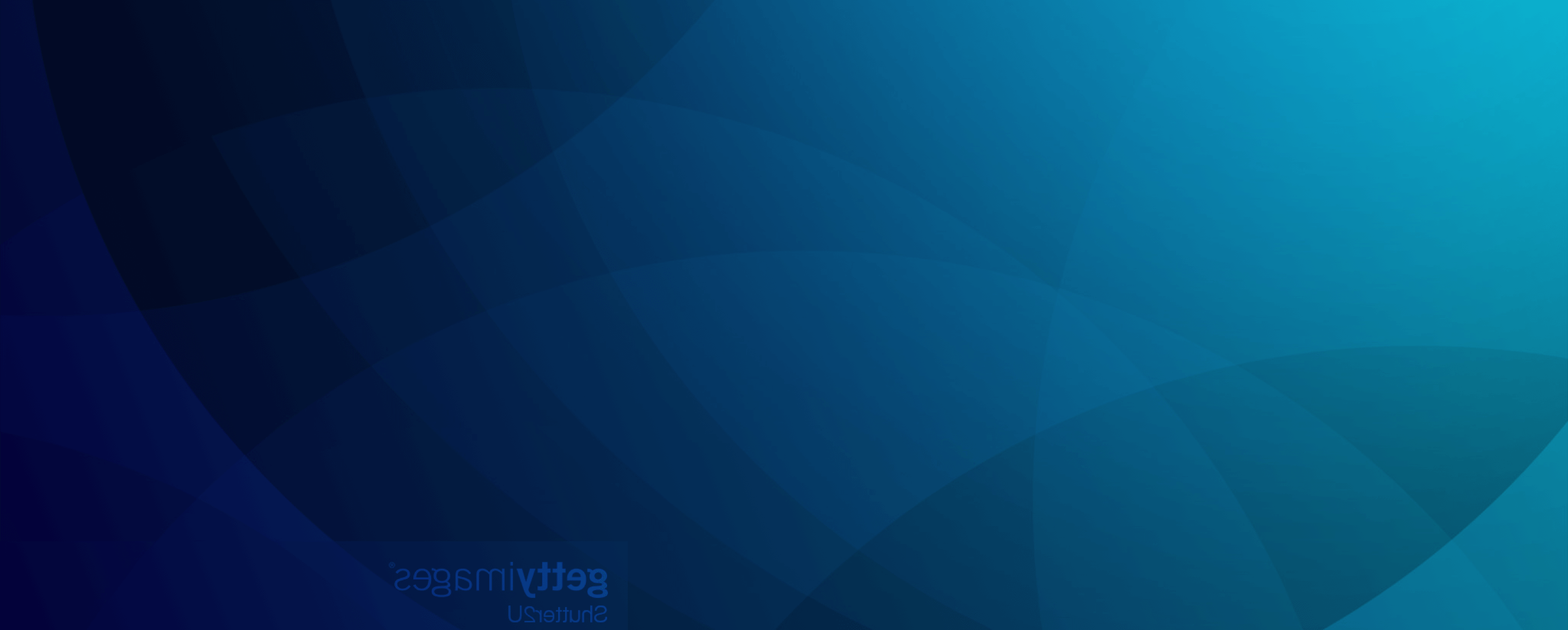