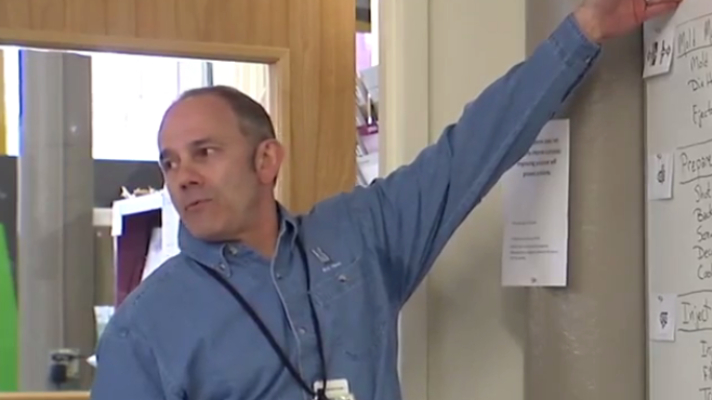
The Challenge
As a MedTech Molder, we utilize multiple high precision molded parts in our assembly automation cells to produce the final medical product that needs to be shipped to stock at the original equipment manufacturer. We needed to minimize the cost of scrap on a high dollar finished device—just one bad part out of a 12-component assembly can cost a lot of money. There is no rework.
In order to address this challenge, we tried standard methods of sticking to the process run sheet set points from run to run. We also implemented the use of the process monitoring features on the machine to identify possible variations. Though the results were good, we always seemed to be chasing something on the higher precision parts with tighter process windows. This was in part due to following traditional process developments instead of a systematic molding approach.
The Solution
In 2001, Doug Thorpe, then a Nypro Project Engineer, attended a local Executive Overview with Rod Groleau, founder of RJG. Thorpe quickly completed RJG Master Molder I and II as well train the trainer. I was a student in Thorpe’s first class at Nypro’s Learning Center in 2003 and became a certified trainer in 2007.
We were so enlightened and recharged by our experience in the course, we decided to continue training our workforce through RJG. All of our technical resources, as well as non-technical, are encouraged to attend some level of RJG training in order to develop a common understanding of the challenges we face as a MedTech (and packaging) injection molder / assembler.
After an initial 15-machine trial in 2004, we have since outfitted our entire fleet of machines with eDART® Systems. We have now been working with RJG for over 10 years, for both training and technology. In that time, we standardized on cavity pressure sensors where applicable and learned a ton as a team. It has been a learning curve to get to where we are today, but it has grown into part of our culture.
The Result
Nypro has since made the use of RJG methodologies a part of our everyday culture, from Systematic Process Development through production process control/monitoring/sort for the final molded part. We have standardized the use of systematic decoupled molding process development and implemented the use of cavity pressure technology part containment. RJG’s technology also allows us to measure and reduce cavity-to-cavity variation.
Utilizing RJG’s technology gave us the ability to see inside the process and understand what was going on. The eDART graphs allowed us to see the interaction of the press and cavity at the same time with respect to plastic pressure. Our customers now have an increased confidence in our capabilities, and we have become the least of their concerns in the supply chain.
Chris Lillyman
Manufacturing Engineering Manager
Nypro Healthcare, Clinton / Devens
About Jabil
Jabil is a product solutions company providing comprehensive electronics, design, production and product management services to global electronics and technology companies. Offering complete product supply chain management from facilities in 29 countries, Jabil provides comprehensive, focused solutions to customers in a broad range of industries.