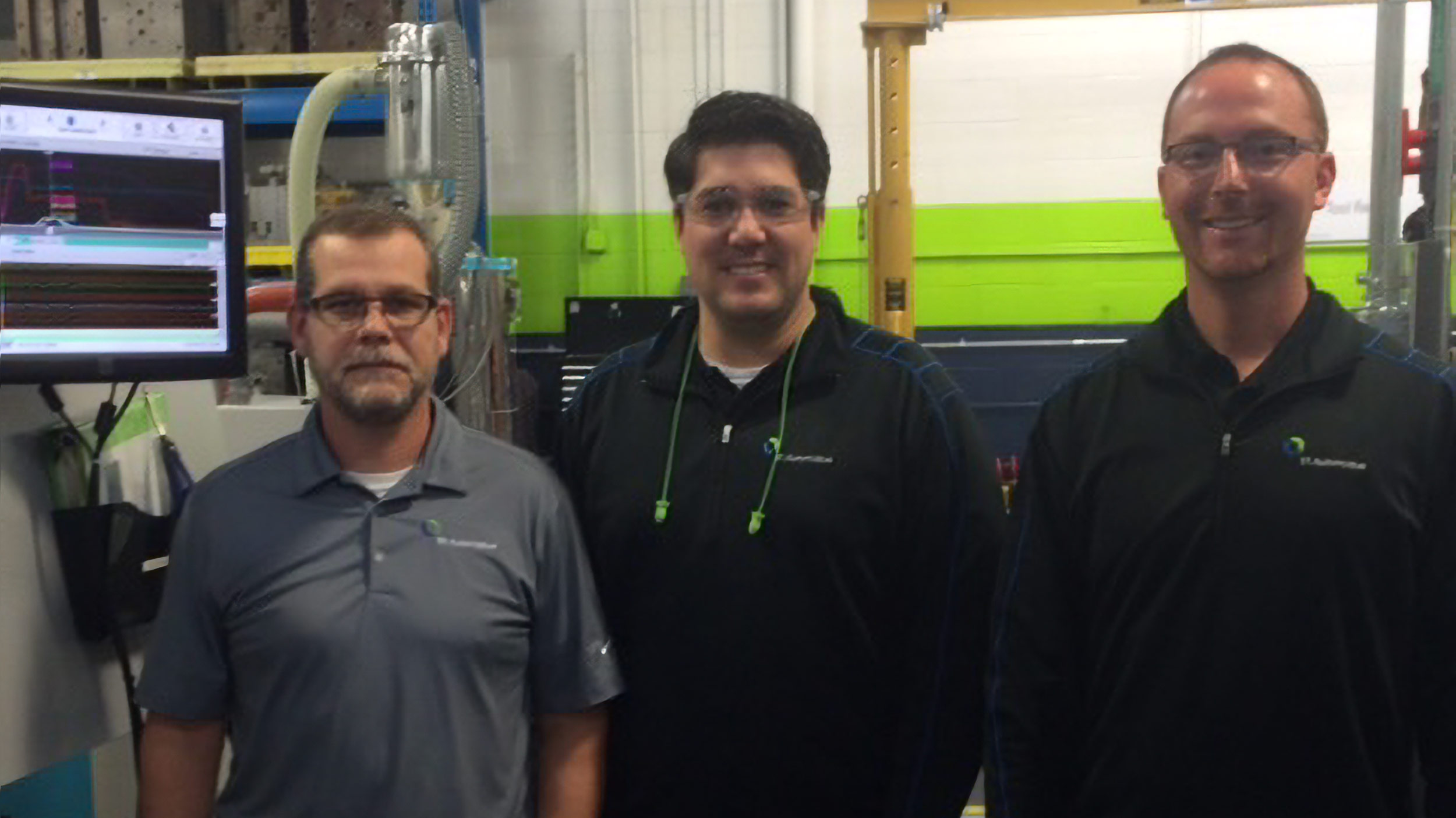
The Challenge
We were faced with three main challenges: short shots, flash, and a lack of understanding the injection molding process. To combat this, four years ago we decided that we would invest in our molding capabilities. We purchased new injection molding machines, new auxiliary equipment, and robots and started investing in all new molds. This was great and helped get us back on track with better quality and output. But there was still something missing.
Our scrap rate was 1.25%. The problem we had was that these parts are a safety and regulatory item that would be carrying fuel on vehicles. We couldn’t accept even one defect that could potentially cause fuel leaks or a dangerous situation in the field. We interfaced a robot with the machine trend chart and did a study to determine if the machine tolerances for the process were sensitive enough to constantly reject a short shot, no matter how small it was. It couldn’t.
Big problem…
The Solution
I have been using RJG methods my entire career. In 1996, my employer at the time sent me to attend my first RJG course: Systematic Molding. Then in 2007, I attended a Master Molder course and received my certificate. Soon after, I started working with large medical devise suppliers to streamline the build and leave no unanswered questions on part integrity based on the established process parameters.
Management was convinced that if we implemented the eDART®, set up all of our molds with end of cavity sensors, and interfaced to the robot, we would effectively capture potential defects as well as force the employees to understand the process and make better processing decisions.
The Result
After 11 injection molding machines and more than 35 molds were equipped with pressure sensor controls, our scrap and efficiency was amazing. Our scrap went from 1.25% to .25%, and our daily output went from 99,000 connectors to 150,000. By establishing tolerances on the end of cavity, we’re able to sort out every defective part before it even reaches the operator.
RJG offers unprecedented technical support, and their hands-on training courses provide a huge amount of helpful information. The level of difficulty and variety of lessons really makes the information stick. RJG has insured that our customers receive a high quality, consistent product that was produced by very competent employees.
Jamey Cates
Senior Process Engineer
TI Automotive
About TI Automotive
TI Automotive develops and produces award-winning, industry-leading automotive fluid systems. For almost 100 years, TI Automotive has provided its technology to vehicles around the world. With more than 120 manufacturing locations in 29 countries, our strength lies in our ability to creatively meet the ever-changing needs of the global automotive industry.